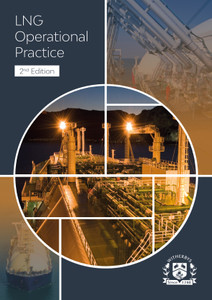
This publication is a technical review of the processes and procedures commonly found in production, storage and transportation of LPG cargoes. It examines the presence of water in LPG cargoes, the formation of hydrates and methods for their elimination.
Hydrate formation in cargo systems of refrigerated LPG carriers can damage pumps and other machinery and obstruct cargo handling. This publication, based on a review conducted for SIGTTO by Mr R C Gray of the Technology Department of British Shipbuilders, deals specifically with hydrates forming in commercially dry refrigerated LPG. It identifies the ways in which water can enter and remain within the cargo, leading to the formation of hydrates. It examines different methods to prevent ice and hydrate formation and outlines procedures for cargo tank sampling. The Appendices provide practical information on the propane-water system, use of LPG freeze valves and the addition of methanol as a treatment method.
Executive Summary
LPG is peculiar in that, certainly at temperatures above 0°C, the boil-off vapour will contain a higher proportion of water by weight than the liquid with which it is in equilibrium. Semi-refrigerated propane at +6°C, for example, containing 40 ppm water by weight in solution, will produce boil-off vapour containing 580 ppm water w/w. The solubility of water in the liquid phase of LPG decreases markedly with temperature.
All refrigerated LPG delivered by a terminal to a ship, while it may be free from ice or hydrates, will contain a small amount of water dissolved in the cargo. While the dissolved water content in the cargo liquid will be low (a few ppm at most), the boil-off vapour will contain a substantially higher proportion of ppm water vapour by weight than does the liquid. In view of the very much higher vapour pressure of LPG compared with the vapour pressure of water, this may seem strange but indications are strongly that this is so. As the hot boil-off gases containing this higher water content are condensed, the majority of the water vapour in the cargo vapour will separate out as particles of solid hydrate. The LPG condensate at the typical condenser temperatures and pressures will contain the remaining concentration of water from the boil-off vapour in solution. However, as the condensate is flashed off via the regulating valve to tank pressure, the resultant further cooling of the condensate will render it unable to hold this higher water concentration as dissolved water, free water will separate out and this free water will form hydrates.
Whilst there is evidence that fully refrigerated propane contains less than 5 ppm water in solution, little information is available concerning the water content in boil-off vapours at temperatures below 0°C. Despite this lack of supportive data, however, there is reason to believe that the boil-off vapour at these temperatures similarly will contain a higher ppm w/w concentration than that in the liquid phase.
Propane may form hydrates at temperatures below +6°C and pressures up to 35 bar and commercial butanes at temperatures below +3°C.
The data available on the water solubilities in liquid and vapour above 0°C lead to a suggested mechanism for the formation of hydrates in vapour recovery systems operating in this temperature range. Operational experience has shown however that such formations can and do occur in vapour recovery systems associated with fully refrigerated propane and despite the present lack of water solubility data available at such temperature, it is assumed that a similar mechanism of hydrate formation applies.
Section 1 of this Study describes how water may be introduced into LPG cargoes during production, storage and transportation. Section 2 addresses the formation of hydrates. It describes how, once hydrate formation is initiated, there is a significant "seeding’’ effect which can block valves and pipelines and gives detailed information on the water content in LPG and vapour. Section 3 proposes how hydrate formation may be avoided or, at least, controlled. Section 4 outlines various test methods for use on board ships. Section 5 describes the potential hazards to the cargo handling system of ice or hydrate formation. Section 6 summarises the results of this Review and outlines recommendations for further research.
Section 1 – Introduction of Water into LPG
1.1 At Production Plants
1.2 During Storage
1.3 On Board Ship
1.4 Hydrostatic Testing
Section 2 – The Formation of Hydrates
2.1 General
2.2 Propane Hydrates
2.3 Butane Hydrates
2.4 Processes in which Hydrate Formation can be Expected
2.5 Modification of Hydrate Formation by Methanol Addition
2.6 Solubility of Water in LPG Liquids and their Vapours
Section 3 – Avoidance of Ice or Hydrate Formation
3.1 General
3.2 Reduction in Water Dewpoint on Ships
3.3 Solid Desiccants
3.4 Hydrate Formation Temperature Depressants
3.5 Hydrate Control Without Methanol Injection
Section 4 – Shipboard Test Methods
4.1 Sampling Methods
4.2 Water Content
4.3 Methanol Detection
Section 5 – Hazards Associated with Ice/Hydrates
5.1 Reliquefaction Units and Cargo Piping Systems
5.2 Cargo Pumps
Section 6 – Summary and Recommendations
6.1 Fully Pressurised LPG
6.2 Fully and Semi-Refrigerated Shore Systems
6.3 Formation of Hydrates on Ships
6.4 Shipboard Counter Measures
6.5 Shipboard Test Methods
6.6 Validation of Data Assumptions
Appendix I – Explanation of the Propane-Water System
1. Why LPG Boil-off Vapour Contains More Water than the Liquid
2. The Vapour, Liquid and Solid Phases of the Propane-Water System during Reliquefaction
2(i) Direct cascade reliquefaction
2(ii) Direct two stage reliquefaction
3. Formation of Hydrates during Vaporisation of Propane Liquid Contaminated with Water
4. Ethane, Iso- and N-Butane
Appendix II – LPG Freeze Valve
Appendix III – Estimation of Methanol to Add to Prevent Ice/Hydrate Formation
A. Methanol to add to a tank containing propane or n-butane saturated with water at 38°C to prevent ice/hydrate formation on cooling down tank contents from SVP at 38°C to atmospheric pressure
B. Methanol to add to the reliquefaction condenser in propane and n-butane duty to prevent hydrate formation in the condenser or in the condensate return
SIGTTO
The Society of International Gas Tanker and Terminal Operators (SIGTTO) is an international body established for the exchange of technical information and experience, between members of the industry, to enhance the safety and operational reliability of gas tankers and terminals. Learn more: https://www.sigtto.org/about-us/
- Number of Pages:
- 50
- ISBN:
- 9781905331277
- Published Date:
- July 2008
- Binding Format:
- Paperback
- Book Height:
- 300 mm
- Book Width:
- 210 mm
- Weight:
- 0.5 kg
- Preview:
- Yes
- Author:
SIGTTO