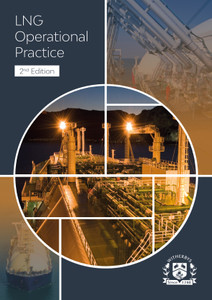
This publication is a guide to the design and development of fully refrigerated LPG carriers.
This book provides a detailed overview of the design and development of fully refrigerated LPG carriers. Each chapter is devoted to a different shipbuilding yard around the world that has been instrumental in the development of transferring liquefied gases in bulk and covers the development of the first fully refrigerated LPG carrier within each yard through to the present day.
Sophisticated ships they may be, but the designs of gas carriers are based on the
simple parameters of the ideal gas laws governing the relationships between pressure,
temperature and volume. In addition, the materials in direct contact with the liquid cargo
must be matched with the properties and characteristics of the cargo. The key to the
designs is the atmospheric boiling temperature of the liquid cargo, i.e. ambient for fully
pressurised LPG, -33°C for anhydrous ammonia, -48°C for propane, -104°C for ethylene
and-163°C for LNG.
LPG carriers can be grouped into three categories; fully pressurised, pressurised and
refrigerated and fully refrigerated. The first ships designed to carry LPG were fully
pressurised and today there are many trading routes where butane and propane are still
transported under pressure at ambient temperature. Almost half of the total number of LPG
carriers in service are small fully pressurised ships, with most operating coastal or island
services in Japanese, Korean, Chinese and Caribbean waters.
The most versatile LPG carriers are the small to medium sized pressurised and refrigerated
vessels, with capacities up to 30,000 m3, capable of loading and discharging a wide range
of LPG and chemical gases. Modern gas carriers of this type are generally designed for
a minimum temperature of -48°C, a maximum pressure of 5 to 8 kg/cm2 and a maximum
specific gravity of 0.97 for vinyl chloride monomer (VCM).
The design of fully refrigerated LPG carriers has evolved over the years from other types
of LPG carriers, to make the most efficient use of the on board cubic space available.
The minimum design cargo temperature is generally -48°C for propane, with the maximum
design pressure 0.25 kg/cm2 greater than atmospheric pressure.
Fully refrigerated LPG carriers have been built with capacities up to 100,988 m3. Apart from
the cargo temperature, the FRLPG carrier has more in common with the LNG carrier than
the smaller pressurised LPG carriers. Much of the extensive research and development
of the late nineteen fifties and early nineteen sixties on LNG carriers also resulted in the
first designs for fully refrigerated LPG carriers.1 There is a considerable overlap of the
techniques which have gone into both the LNG carrier and the FRLPG carrier, each with
many similar design features. Throughout the gas ship building industry the learning curve
has been gradual with yards progressing to larger vessels after cutting their teeth on smaller
ships. Most yards with fully refrigerated LPG ship building experience moved on into the
LNG market. A notable few exceptions were; Harland and Wolff, Chantiers de France
Dunkerque, Boelwerf and Daewoo, who took the reverse approach and started with LNG
carrier construction.
When comparing the construction of the first purpose built fully refrigerated LPG carrier,
Bridgestone Maru, delivered from MHI in 1961, with a typical modern FRLPG carrier,
the differences in general appear to be slight rather than radical. This was not so in the
decade following the delivery of Bridgestone Maru, particularly in Europe, where ships
were delivered with a selection of tank shapes and insulation arrangements. A popular
arrangement on many earlier ships included above deck trunks, allowing an increase in
cargo capacity without any increase in hull dimensions. With experience, the shipbuilders
found that the tanks with trunks were not so easy or cheap to construct, particularly with
the increased number of the tanks’ radius edges and part spherical shaped corners.
Naval architects quickly realised the advantages of constructing FRLPG carriers with a flush
deck, with longitudinally framed sloping upper and lower wing ballast tanks at the sides
and a transversely framed side hull forming the secondary barrier. This arrangement, which first appeared on 25,540 m3 Antilla Cape, delivered from A. G. Weser in 1968, has now
become almost the standard configuration for the modern FRLPG carrier. In fact, every fully
refrigerated LPG carrier delivered since 39,113 m3 Kelvin, from IHI in 1990, has had this
arrangement for cargo tanks and water ballast tanks. The IHI ship had a slight variation on
the standard arrangement by having the inner bottom extending to the side hull to form the
lower water ballast tanks.
In 1976, the Code for the Construction and Equipment of Ships Carrying Liquefied Gases in
Bulk was first published by the then Inter-Governmental Maritime Consultative Organization
(IMCO). For the first time, the Code set out international standards for the safe carriage of
liquefied gases in bulk.
From the time of the first meeting, in September 1971, of an Ad Hoc Working Group
within IMCO 2, until the Code was published in 1976, shipbuilders were well aware that the
pending Code would require changes to the design of FRLPG carriers. As it turned out,
wholesale changes were not required to existing practices, rather a fine tuning of layouts
and tank locations within the ship, with extra safety, fire-fighting and monitoring equipment
added. The main areas requiring changes were; damaged stability requirements, cargo
tank and ballast tank locations, segregation of the cargo area, openings in accommodation
spaces and fire protection systems.
The new Code had more radical effects on the design of smaller LPG carriers than on larger
LPG carriers. In the intervening years the Code has been reviewed, revised and amended.
The 1993 edition published by the International Maritime Organization (IMO), became the
International Code for the Construction and Equipment of Ships Carrying Liquefied Gases
in Bulk (IGC Code).
A number of the earlier built LNG carriers were designed to carry both LNG and LPG,
as no long term LNG trading had yet been fixed at the time of ordering, and the spot
LPG market offered opportunities for employment of the ships. Some of the smaller LNG/
LPG carriers were also able to load ethylene. Few traded with LPG cargoes and detailed
descriptions of these ships have not been included in this book, as the ships are primarily
LNG carriers. One technical point, which may have contributed to the remarkable life span
of these vessels is that the carriers were designed for a propane specific gravity of 0.58.
This represents a considerable margin of safety when loading LNG with a specific gravity
of 0.44.
The following is a brief summary of the combined LNG/LPG and LNG/LPG/ethylene carriers
built:
• Esso Brega now LNG Palmaria – 41,000 m3 with Esso prismatic tanks built at Italcantieri, Genoa, Italy in 1969 and modified to carry LPG at Moss Rosenburg, Stavanger, in 1976.
• Descartes – 50,000 m3 with Technigaz membrane tanks built at I’Atlantique, St. Nazaire, France in 1971.
• Euclides – 4,000 m3 including ethylene, with Technigaz spherical tanks built at Le Havre in 1971 and broken up as Chem Unity in 2002.
• Norman Lady and LNG Challenger now Höegh Galleon – 88,000 m3 with Moss spherical tanks built at Moss Rosenburg, Stavanger, Norway, in 1973 and 1974.
• Venator now Havfru and Lucian now Century – 29,000 m3 including ethylene, with Moss spherical tanks built at Moss Værft, Norway, in 1973 and 1975.
• Ben Franklin – 120,000 m3 with Technigaz membrane tanks built at La Ciotat, France, in 1975.
• Kentown now Isabella and Montana now Annabella - 35,400 m3 with Gaz Transport membrane tanks built at CNIM, La Seyne, France, in 1975.
• Hilli, Gimi and Khannur- 126,000 m3 with Moss spherical tanks built at Moss Rosenburg, Stavanger, Norway, between 1975 and 1977.
• Mostefa Ben Boulaid - 125,000 m3 with Gaz Transport membrane tanks built at La Ciotat, France, in 1976.
• Sant Jordi - 5,000 m3 including ethylene, with Sener spherical tanks built at Tomas Ruiz, Spain, in 1976 and sunk as Red Star on 6 January 1994.
• Gastor now LNG Lagos and Nestor now LNG Port Harcourt - 122,200 m3 with Gaz
Transport membrane tanks built at I’Atlantique, St. Nazaire, France, in 1976 and 1977.
• Golar Freeze and Höegh Gandria - 125,000 m3 with Moss spherical tanks built at HDW, Kiel, Germany, in 1977.
• Mourad Didouche and Ramdane Abane - 126,000 m3 with Gaz Transport membrane tanks built at I’Atlantique, St. Nazaire, France, in 1980 and 1981.
As an introduction to the construction and layout of a typical fully refrigerated LPG carrier, the next chapter will take you on board such a ship.
Preface
Introduction
List of Figures
List of Plates
Glossary
Bibliography
About the Author
1. Virtual On Board Inspections
2. French Refrigeration Breakthrough
3. Japanese Pioneers Bridgestone and Mitsubishi
4. First Refrigerated LPG from Ras Tanura Terminal
5. Secondary Barrier Side Hull from A G Weser
6. Conversion and New Buildings from Hitachi Zosen
7. European First from Kockums
8. Verolme Pair for the Ammonia Trade
9. Home Town Shipyard Hawthorn Leslie
10. LPG and LNG Technologies Intertwined at IHI
11. Moss Vaerft and Dokk
12. Scottish Ammonia Carrier Conversion
13. Single Invar LPG Membrane from CNIM
14. Spanish First from Euskalduna
15. Single FRLPG Carrier from Kiel
16. Conversions and Combined Carriers from the USA
17. Semi-Membrane Kasmet from Kawasaki
18. Thyssen Nordseewerke Four for P&O
19. Large and Small from Italy
20. Boelwerf’s Entrepreneurial Audacity
21. French Connection for NKK
22. Scottish Roots for Hyundai Plants
23. Pioneering French Connection at Daewoo
24. New Fully Refrigerated LPG Carrier Design Concept – Ptarmigan
Appendices
1. Delivery Chronology
2. Original Names
3. Current Names
4. Capacity
5. Lead Ship Dimensions
6. Shipbuilders
7. Previous Names
8. Name Changes
Index
Syd Harris
Syd Harris was an independent consultant in naval architecture and marine surveying for over 35 years. A fellow of the Royal Institution of Naval Architects, a Chartered Engineer and a Member of the Society of Consulting Marine Engineers & Ship Surveyors, he specialised in gas shipping and worked closely with both SIGTTO and Gastech throughout his career.
- Number of Pages:
- 314
- ISBN:
- 9781856092661
- Published Date:
- May 2004
- Binding Format:
- Hardback
- Book Height:
- 304 mm
- Book Width:
- 215 mm
- Weight:
- 1.4 kg
- Preview:
- Yes
- Author:
- Syd Harris